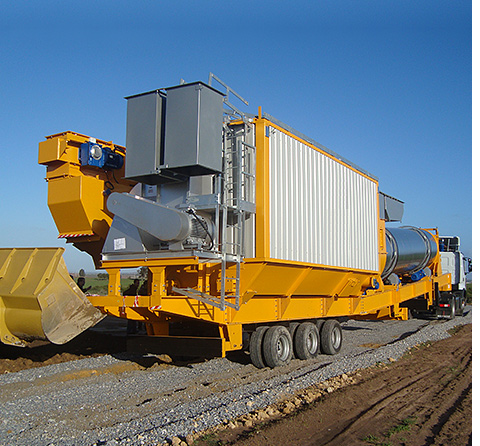
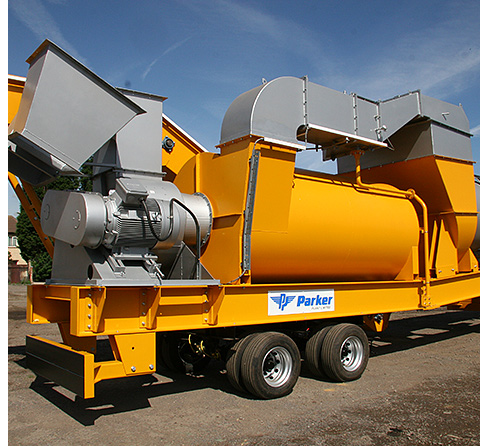
DrumStar
Continuous Drum Mix Asphalt Plants
An economical and highly portable alternative to batch mixing plants, with capacities of 75, 100, 150 & 200 TPH.
The 75 & 100 TPH models are designed to be containerised for ease of transportation.
- Fully mobile road towable units
- Minimum foundations required
- Fast on-site erection
- Factory pre-wired & fully tested
- Inverter controlled exhaust fan
- Dust emissions less than 20mg/Nm3
The DrumStar range of continuous asphalt mixing plants offer an economical and highly portable alternative to batch mixing plants for use in approved locations.
Contractors enjoy quick site relocation with total mobility while retaining the ability to maintain high levels of quality asphalt production. A choice of capacities includes 75, 100, 150 and 200 tph and the chassis of the two smaller models is designed to be unbolted for transport across the world within standard containers.
Each plant has the options of either bag filter or wet collector dust control depending on the restrictions of the contract and its location. The plant can be supplied complete with mobile or static bitumen tanks and all associated pipe work and pumps as well as reclaimed or imported filler storage silos.
Features
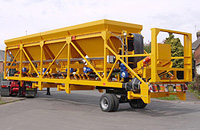
Cold Feed
Road towable, multi-hopper, cold feed unit with built in collecting conveyor and dryer feed conveyor with roll out scalping screen. Direct drive geared motor units give high reliability. Accurate variable speed control via AC motor and inverter.
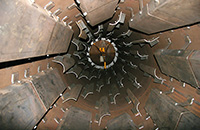
Drum Mix
The dryer drum features a unique lifting pattern to cascade the material through the hot air stream. Bitumen and fillers are added at the drum discharge end. Steel support rollers are provided to allow for sudden plant stops.
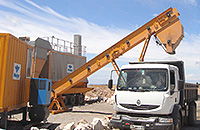
Drag Slat Conveyor
Mixed material is transferred by the drag slat for direct lorry loading. A 3 tonne batch hopper with pneumatic rotary door allows sufficient time for trucks to transition.
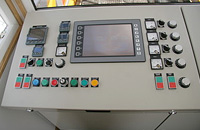
Controls
Comprehensive key-pad PLC controls with full alarm diagnosis can be either plant mounted or optionally cabin installed.
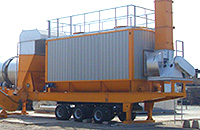
Dust Filter
Dust laden air can be filtered through a fabric filter where environmental legislation demands. Mounted on the main chassis, the exhaust fan draws air through specially designed fabric filter bags. Collected dust is screwed back into the mixing section of the drum.
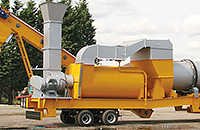
Wet Collector
Where emission regulations are not as stringent a wet collector option can be supplied. Coarse dust is removed in an expansion box with finer dust particles being passed through a water spray. The resultant residue is screwed to a collection pit
Specifications
Units | DS75 | DS100 | DS150 | DS200 | |
Plant Capacity | |||||
Output* | tph | 75 | 100 | 150 | 200 |
Cold Feed | |||||
Hopper Capacity (heaped) | m³ | 10.0 | 10.0 | 14.0 | 14.0 |
Hopper Loading Width | m | 3.0 | 3.0 | 3.5 | 3.5 |
Belt Feeder Length | m | 1.7 | 1.7 | 1.7 | 1.7 |
Belt Width | mm | 500 | 500 | 650 | 650 |
Belt Feeder Drive | kW | 2.2 | 2.2 | 3.0 | 3.0 |
Vibrator Fitted to Sand Hopper | YES | YES | YES | YES | |
Collecting Conveyor Width | mm | 650 | 650 | 650 | 650 |
Collecting Conveyor Drive | kW | 4.0 | 4.0 | 5.5 | 5.5 |
Scalping Screen Size | mm | 800 x 1200 | 800 x 1200 | 1000 x 1200 | 1000 x 1200 |
Scalping Screen Drive | Watt | 2 x 300 | 2 x 300 | 2 x 300 | 2 x 300 |
Aggregate Dryer | |||||
Slinger Conveyor Width | mm | 500 | 500 | 650 | 650 |
Slinger Conveyor Drive | kW | 3.0 | 3.0 | 4.0 | 4.0 |
Dryer Drum Diameter | m | 1.4 | 1.6 | 1.8 | 2.0 |
Dryer Drum Length | m | 7.0 | 8.0 | 9.0 | 10.0 |
Dryer Drive | kW | 4 x 5.5 | 4 x 7.5 | 4 x 11.0 | 4 x 15.0 |
Air Volume | |||||
Total | m³/h | 22,500 | 30,000 | 45,000 | 60,000 |
Burner | |||||
Burner Type | PB1A | TJ02 | TJ03 | TJ03 | |
Capacity | l/hr | 727 | 954 | 1680 | 1680 |
Drag Slat Conveyor | |||||
Slat Width | mm | 400 | 400 | 500 | 500 |
Capacity | tph | 90 | 120 | 170 | 220 |
Drag Slat Drive | kW | 7.5 | 11.0 | 18.5 | 22.0 |
Batch Hopper Size | t | 3.0 | 3.0 | 3.0 | 3.0 |
Bag Filter / Wet Collector | |||||
Filter Area | Sq/m | 260 | 347 | 527 | 702 |
Filter Velocity | m/min | 1.44 | 1.44 | 1.4 | 1.4 |
Filter Exhaust Fan | kW | 30.0 | 45.0 | 75.0 | 90.0 |
(Option) Venturi Wet Collector Fan | kW | 55.0 | 75.0 | N/A | N/A |